Individual elements of undercarriage:
track chains, comprising of, among others: chain pins and sleeves that are subjected to careful grinding and inductive quenching process, as well as chain links that are cast from special steel and subjected to deep inductive quenching proces,
sprockets are cast from a special steel, and then inductive-quenched to obtain maximum abrasion resistance,
idlers comprise of specific material fractions adequately distributing load and tension; they are induction quenched,
track and support rollers are made of special steel, subjected to accurate grinding, and to inductive quenching,
track plates, additionally subjected to thermal treatment.
Track chains
Chains may be divided into the following types:
sealed, sealed and greased, sealed and lubricated (also referred to as self-lubricating). With this categorization in mind, attention must be brought to another important feature that is chain faster method, which is either done using pin with pads, using t-pin, or using a split link (the most user-friendly method of assembly or disassembly a chain). Here it should be mentioned that the first two types are normally used in excavators, and the third type is used in bulldozers. Our offer includes mainly the two latter types of chains, since the use of grease and seals in the chain extends its life by about 20%, whereas the use of oil and seals extends its life by about 50%.
Moreover, the seals used in the chains sold by us not only prevent outflow of grease outside the chain, but also prevent penetration of contamination from outside.
Track chain faster method is also important. The most ergonomic and quickest one is the one employing a split link, which is principally applied in oil chains. This solution allows for a very user-friendly assembly and disassembly of chains, with the use of commonly available tools. Greased chains, on the other hand, employ a pin facilitating the assembly and disassebly of the chain. This solution definitely facilitates faster of track chain, compared to standard pin. Naturally, various modifications beyond the chain types described above are possible, including chains with revolving sleeves, or the CAT-patented System One.
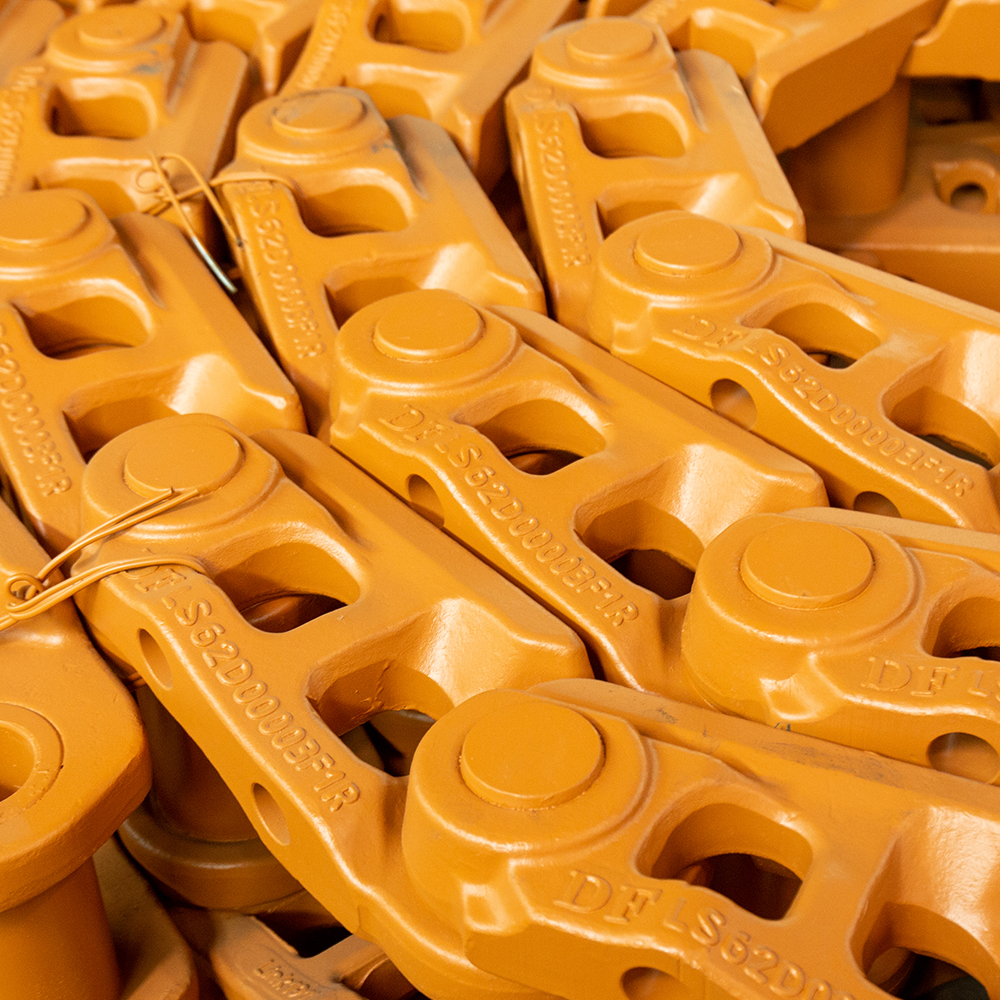
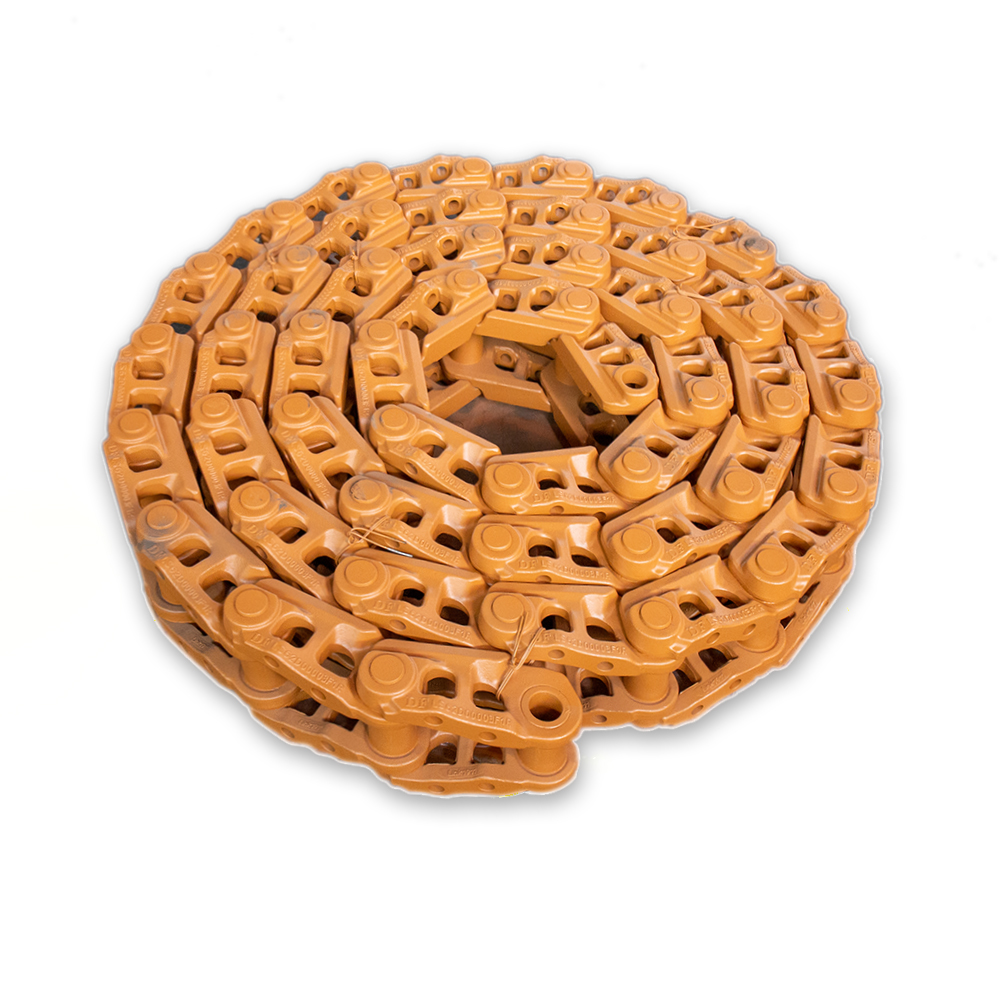
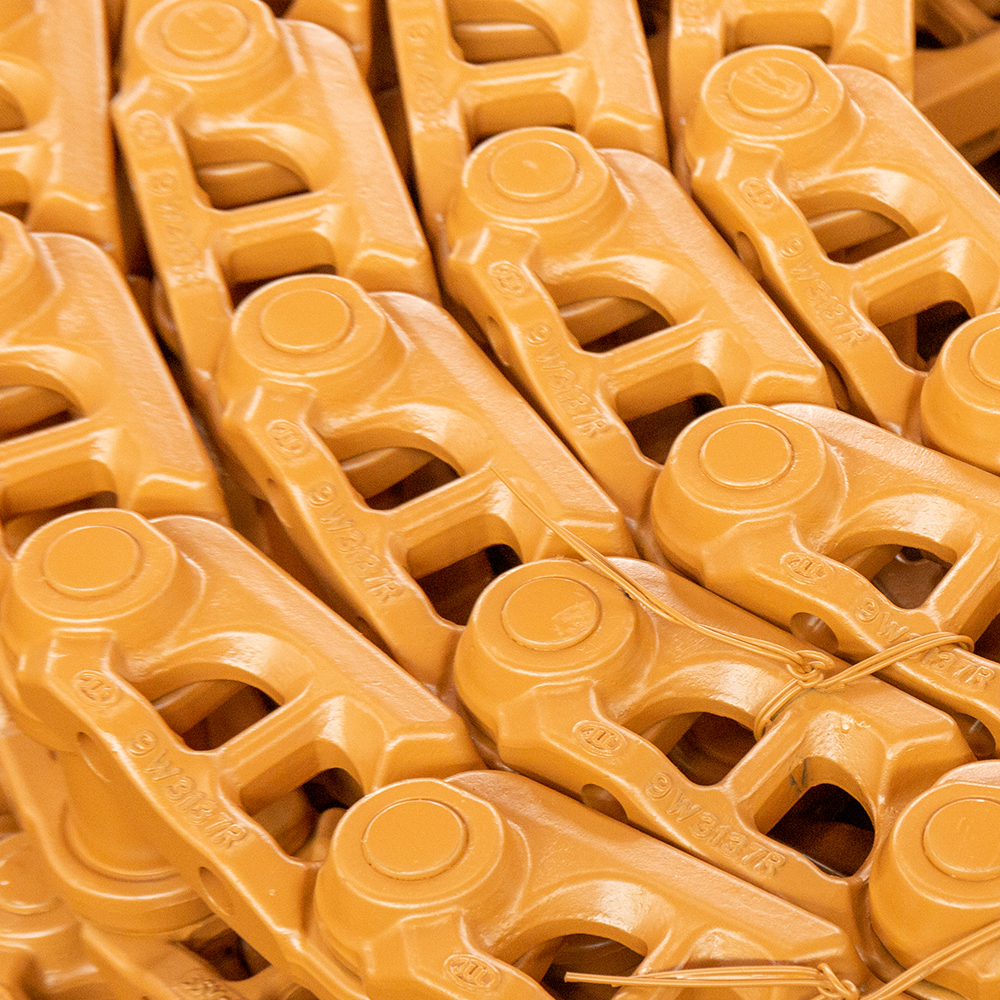
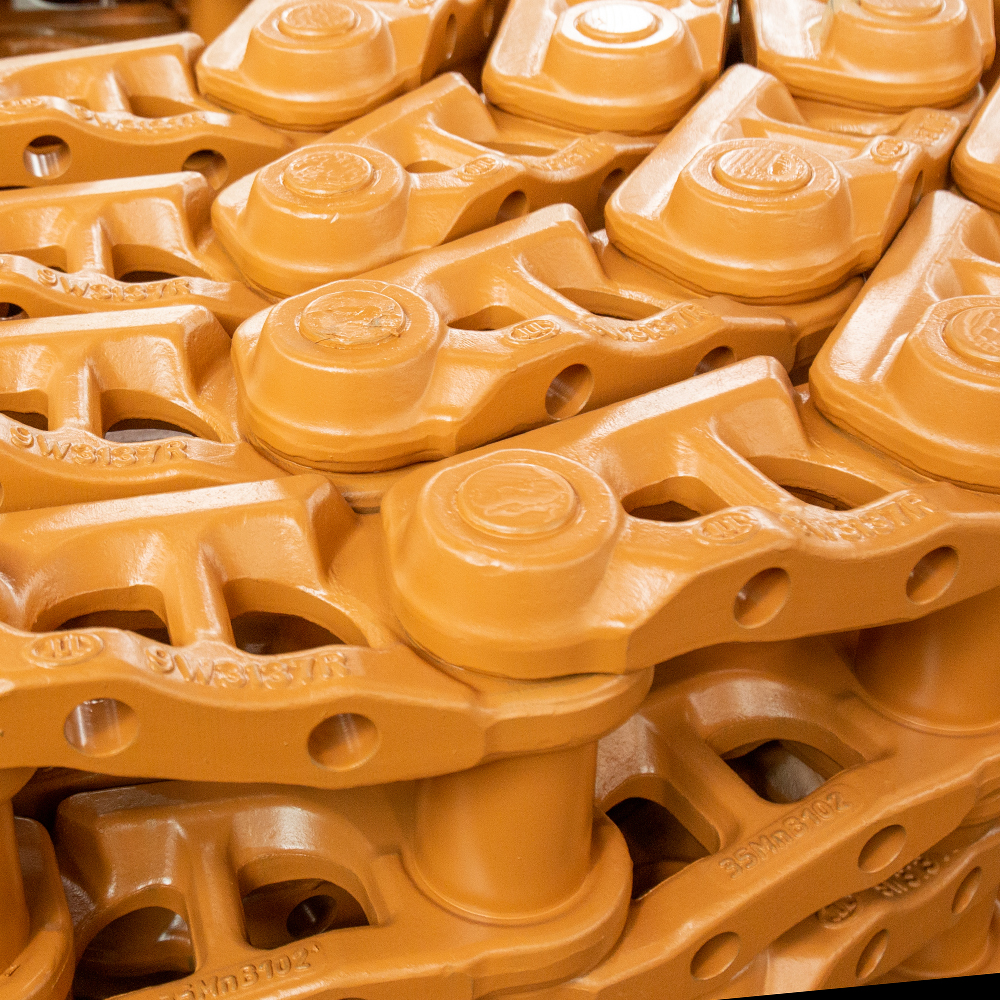
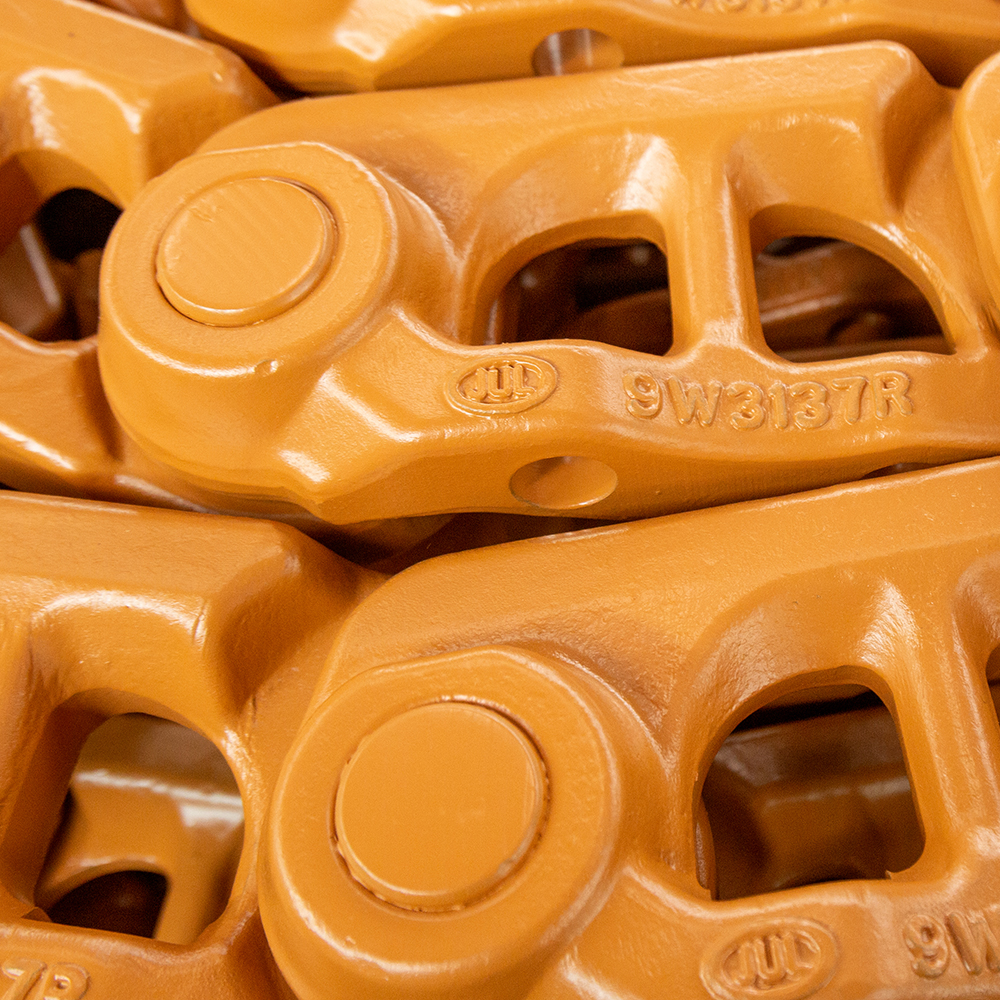
Track plates
Track shoes allow tracked vehicles to operate on various terrain. Depending on the type of application, the plates come with a single, double or triple grouser. Triple-grouser shoes are used in excavators, double-grouser ones are used in tracked loaders, and single-grouser ones are used in bulldozers. Depending on the type of terrain and weight of the machine, the track shoes may be up to 1200 mm wide. It should be noted that the plates offered by us are manufactured of appropriate steel subjected to thermal treatment to ensure maximum abrasion resistance.
Sprockets and idlers
The vast majority of the sprocket are designed in a way allowing to throw earth or other medium off in order to minimize abrasion between the sprocket and the track chain. Precise treatment and appropriate quenching process are very important for this units.
Idlers, especially ones used in bulldozers, are made of different fractions of materials and joined in the process of precision welding. Thanks to the application of different material fractions, they are particularly resistant to torsion and any types of deformations. Moreover, the parameters obtained in inductive quenching process allow for long and reliable service, which is also ensured by the use of tight and self-lubricating revolving motion connection.
Track rollers and support rollers
Particularly important elements of the whole undercarriage system are also tracked and top rollers. At present, manufacturers employ rollers that are pre-filled with oil for their entire life. Maximum resistance to abrasion of the undercarriage elements mentioned is obtained due to the use of adequate castings, precision machine treatment and inductive quenching.
Additionally, very good parameters are obtained due to tempering, which increases durability and extends life of rollers, ensuring their even wear. Principally, rollers used in excavators and in bulldozers differ in their external design. Besides, despite their internal design being basically identical, bulldozer rollers are built more massively, guaranteeing extended life.
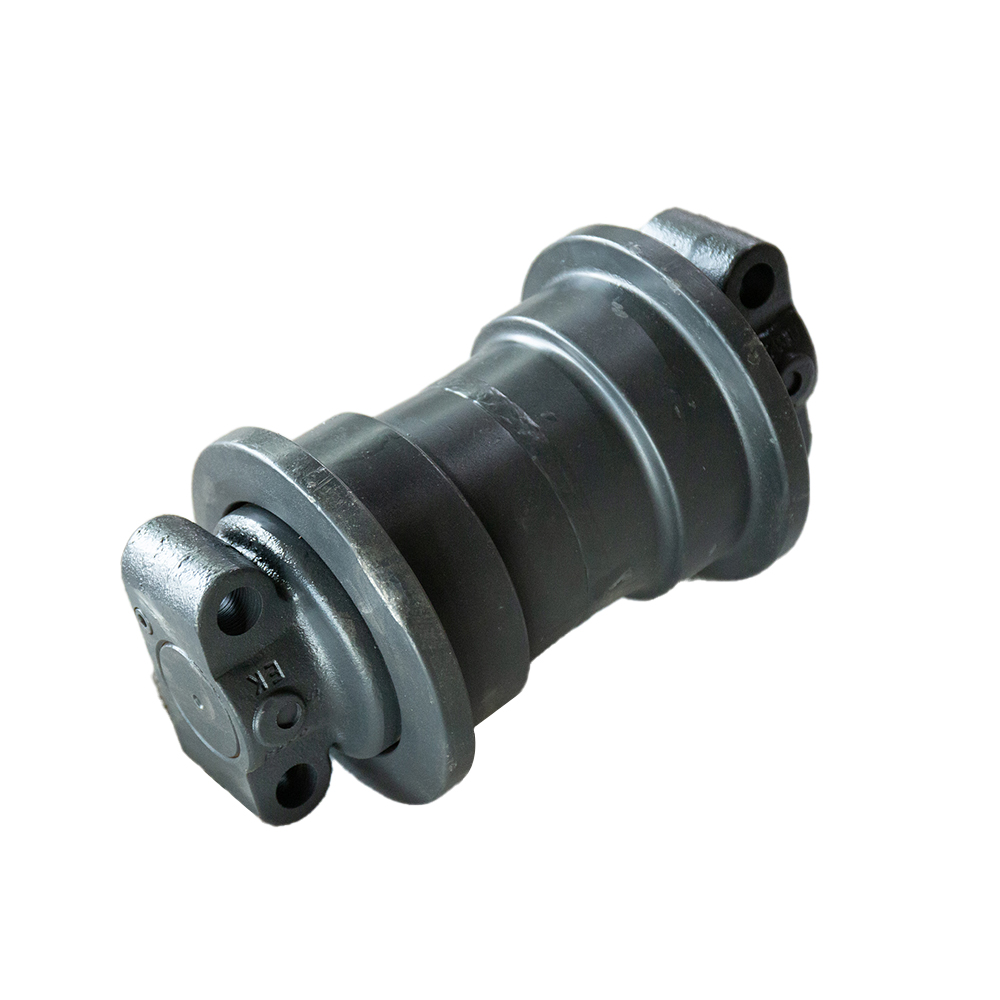
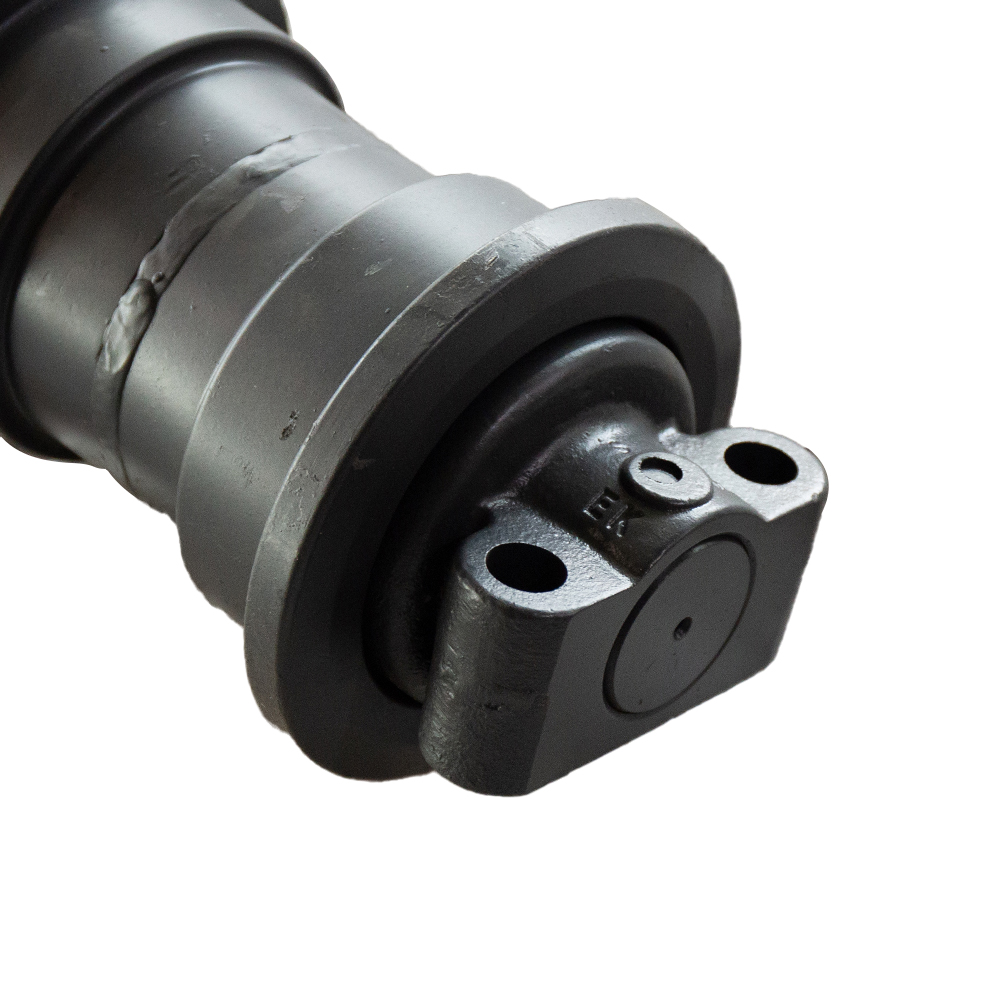
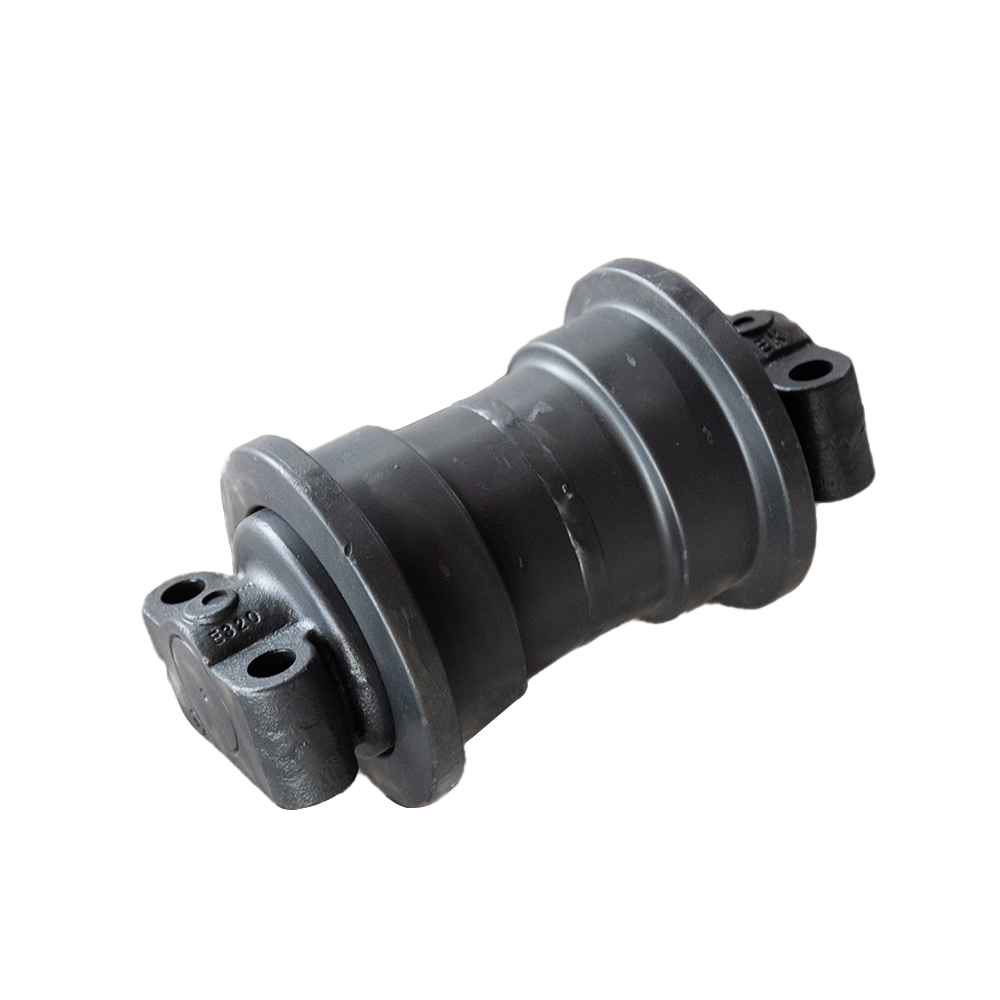
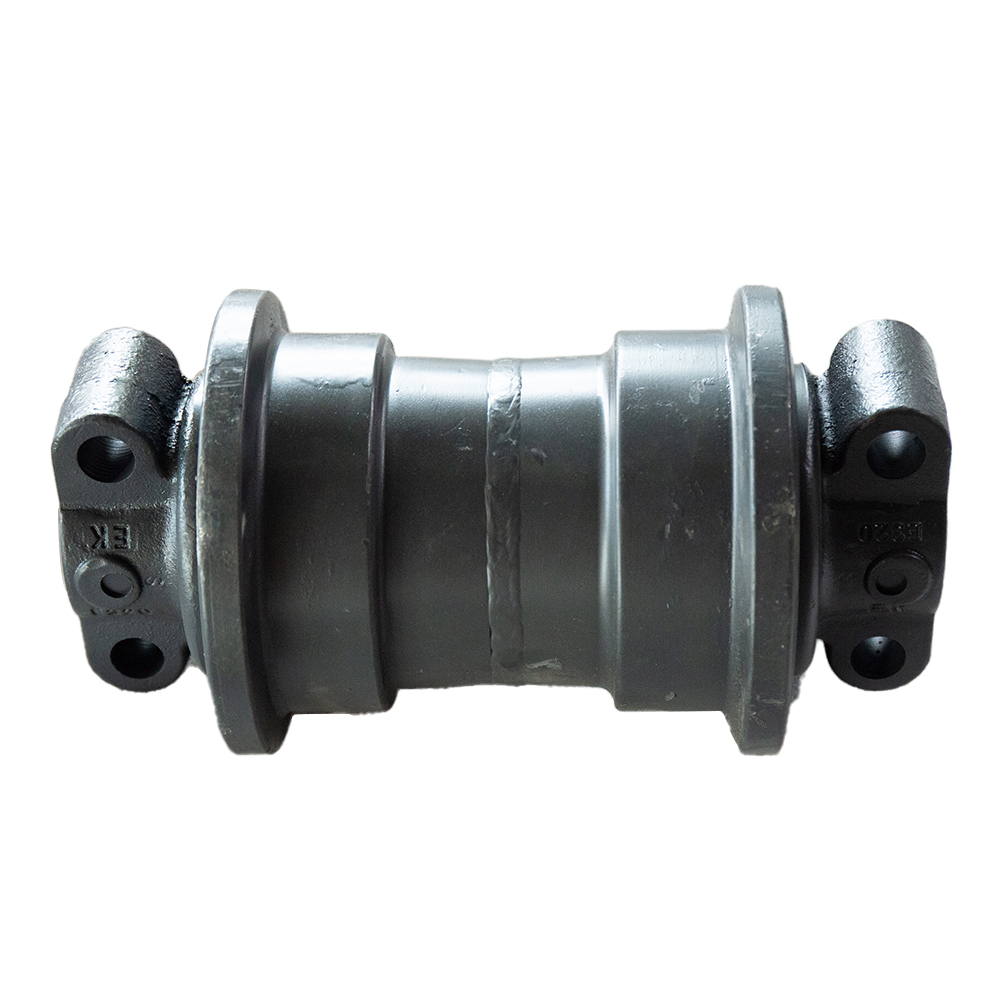